Our Predictions: 4 Industrial Trends for 2024
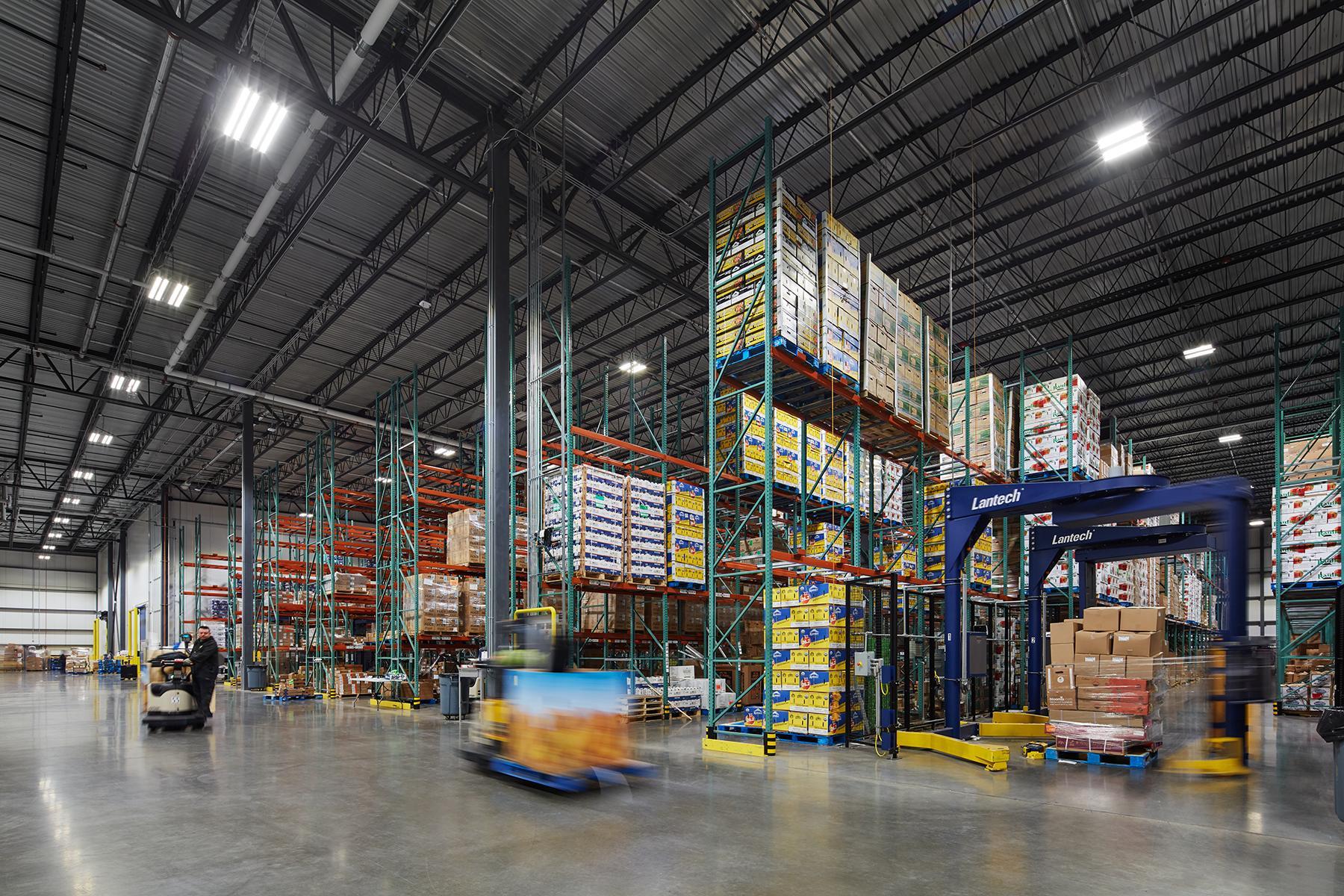
By: Todd Schell, Executive Vice President, Industrial
The supply chain industry continues to adapt thanks to the development of new technologies and updated processes to manufacture and distribute products. To align with these industry trends, Ryan’s approach to industrial facilities—from design to location to product considerations—is also constantly evolving and adapting to the needs of our clients.
So what does that mean for the development, design and construction of industrial facilities?
As we peer into the industry glass ball for 2024, here are the top trends we predict to see in Industrial this year.
1. New focuses: Aviation and Ready-to-Eat Food and Beverage.
The Aviation world is one area stirring excitement at Ryan. Why? Opportunity and need. For the past 20 years, much of the focus within aviation was aimed at improving the overall passenger experience and creation of updating the front of house” at airports. Think security upgrades, airline clubs, terminal design, updated aesthetics and amenities, improved traffic flow and parking, etc.
By proxy, another side of aviation that is more aligned with the “back of house”—has seen less prioritization. In addition, the need to expand aviation related manufacturing has been increasing for several years, as several hundred orders for new aircraft have been committed to growing fleets.
To adapt to these needs, we see a shift in focus from passenger related priorities to “back of house” airport operations and offsite manufacturing including:
- Maintenance, Repair, Overhaul (MRO)
- Cargo operations
- Ground Support Operations
- Supply chain components
Food and Beverage process/manufacturing, specifically for ready-to-eat food products, is another strategic area of growth for Ryan as more businesses are offering these products to consumers. These facilities focus on food production in a Good Manufacturing Process (GMP) environment that prioritizes cleanliness and food safety. From a location standpoint, it is ideal for these facilities to remain close to the local food producers to keep the food as fresh as possible and to take advantage of locally sourced ingredients.
2. An increase in middle mile, smaller distribution facilities in population centers vs. one giant center in between big cities.
To get products to your doorstep and beyond, companies are prioritizing the development and enhancement of their logistics networks. They are now factoring in the many moving parts that have shifted due to the pandemic and e-commerce coming into play. Many companies are trying to figure out the most efficient way to deploy their capital to develop facilities that support their unique growth strategies. Flexibility is key.
As supply chain companies focus on how best to support their unique growth, honing in on key information is essential to making an informed decision on where to develop and build. Key questions include:
- What does the labor pool look like in various locations?
- Where do we need to have the facilities so we can get to the most people?
- Is our strategy based on one hour delivery, one-day delivery, two-day delivery, all of the above?
- What should that facility look like? Should we have three smaller facilities or one large one?
- How can we reach our customers in the best way?
- How does our brick-and-mortar side of the business complement the fulfillment side of the business?
- Is there a hurdle with community buy-in within rural locations and suburbs in particular?
These questions help to define goals and determine the best approach to determine the location and creation of new industrial facilities.
3. Updated cold storage facilities.
Another 2024 prediction is an increased demand for new cold storage facilities, likely buoyed by a future downward trend in interest rates. Why? Because cold storage buildings are outdated, as many of them are more than 50 years old.
Throughout the last 40+ years, food production has evolved. Companies improved food storage processes, how to avoid spoilage and help transport food. The industry grew. Back then, the new facilities were state of the art. But things have changed, and technology has advanced—which is why the facilities need to now upgrade, as well.
Here’s an example: back in the 70s and 80s, the ceilings were lower because it wasn’t practical to have a palette 12+ feet off the ground; there wasn’t material handling equipment (MHE) to reach it. But now, a forklift can go 40+ feet and pick up a palette safely. So there’s the consideration for going higher. Also, with new MHE technology improvements, material handling systems have become more complex and efficient, and the facilities need to be designed to support the automated systems.
Another difference between then and now is, back then, land was cheaper around the country. Now it’s expensive and there is heightened competition, so taking a smaller piece of land and building a taller building can be more cost effective.
4. Improved warehouse design aesthetics.
From an aesthetic standpoint, people who aren’t in the industry hear the word “warehouse” and generally think it’s an unsightly, pre-engineered metal building. Dilapidated. An eyesore on the community. But that’s not really the way industrial is built these days.
Yes, there are some basic, plain warehouses that still exist, but city codes, constraints and ordinances have encouraged the creation of more aesthetically pleasing warehouses. The city often can place requirements that a new warehouse can only be a maximum of 60 feet high and refrain from looking like a huge wall of concrete, for example.
The industry has evolved to reflect intentional design elements within distribution centers, warehouses and more by using several design strategies and tactics. A few examples:
- Recessed reveals. If it is a nonrefrigerated building, recessed reveals are utilized to break up the concrete. Nearly 80% of the time, it is precast concrete or site cast is used along with architectural design and little reveals to break up that wall of concrete.
- Windows. Clear story windows are great for operations and give a better experience for employees; it also adds an element of intentionality and design.
- Covering of concrete panels. To eliminate the drab look of endless concrete panels, adding a different material on the outside of the concrete—such as wainscot or stone—can make a huge difference. Similarly, a warehouse building can be designed to have a roof that has variance in peaks and valleys on top, rather than a thousand feet of flat line on the roof.
- Environmentally conscious design. Designing and building a facility that is more environmentally responsible is important. As more communities are in tune with this evolution, the industry considers such sustainability practices and environmental impact by prioritizing waste reduction and using sustainable materials. Incorporating the use of solar panels and generating power on site (or cogeneration, a more sustainable way of providing energy to a facility) are intentional methods to reduce the impact on the environment. Carbon neutrality—or reducing carbon emissions— is a priority within the industry that helps to save energy and protect the planet.
- Color. Utilizing color on the building exterior helps incorporate visual interest and brighten up the look of the facility. It also adds dimension, reduces monotony or similarity of building aesthetics, and infuses a unique identity differentiator that people can easily see.
Industrial facilities are no longer large warehouses and concrete eyesores that simply store products. This next year will be an exciting one as the industry continues to shift and evolve with the world’s wants, needs and priorities: from an efficiency perspective, a safety standpoint, a sustainability standpoint and a design standpoint. At the end of the day, adaptation is key, and collaboration is necessary.
CONNECT WITH US
Contact Todd for your Industrial project needs